At NC SERVICE we can restore your used CNC milling machine to its optimal operating conditions, by either re-establishing or even upgrading its original performance and functionality, in order to lengthen its useful life optimise its productivity and, in short, improve its market competitiveness.
At NC SERVICE, we are specialists in CNC milling machine retrofitting work, something which we have progressively improved and promoted right from the outset, to become a benchmark company within the sector. Our origins and track record, with regard to the production process and the installation process and Technical Support Service, has led to a high degree of skill and specialisation of our Engineering Department in retrofitting and upgrading milling machines, and the CORREA and ANAYAK brands in particular.
The milling machine retrofitting service offered by NC SERVICE, involves the disassembly and removal of mechanical, electrical and electronic functional parts and sub-assemblies, which due to either wear or deterioration, must be inspected and either repaired or replaced. These operations are performed by our highly-skilled personnel , always following the technical recommendations of the manufacturers, using original spare parts, and the most suitable documentation, tools and techniques for each specific case, required to restore the original reliability and robustness of these milling machines
At NC SERVICE, all these operations are agreed with our customers beforehand, in addition to the components to be replaced during the milling machine retrofitting process, perfectly adapting ourselves to our customers' requirements and thereby shortening the lead times in relation to the purchase of a new machine on the market. We can even locate on the market, the milling machine most suited to the requirements of each customer, and then customise the retrofitting service.
Milling machine retrofitting stages:
1 Study and initial valuation of the machine condition

The milling machines to be retrofitted are received at the NC SERVICE facilities, where an initial analysis is made of their general condition. Based on this initial analysis, and on any considerations relating to the brand, model, structure, production life and other characteristics of the milling machine, we prepare reliable upgrading and retrofitting projects, planning the actions to be taken in addition to the resources and spares required, in order to minimise the execution time for all these tasks.
We are also prepared to go to our customers' facilities, in order to study the situation and make an initial prior technical and financial valuation. This will allow the customer to assess in greater detail the suitability of the retrofitting work required to return the milling machine to its original performance with regard to productivity and reliability.
2 Disassembly of the structural components

At NC SERVICE, once we have received a milling machine to be retrofitted, the first stage is to position it in our workshop where the corresponding tasks are to be performed. These tasks start with the disassembly and removal of all the milling machine functional parts and sub-assemblies which, given their wear or damage, need to be inspected, repaired or replaced. All the mechanical parts on each shaft (X, Y, Z) are dismounted, such as slides, bed, spindles, bearings, head, etc. in addition to electrical, electronic and control parts.
In each case, our Engineering Department uses the most appropriate documentation, tools and techniques, as directly recommended by the manufacturers. If a part needs replacing, then original spares are used. In short we adopt all the measures required to restore the general functionality of the milling machine to optimal conditions of productivity.
3 Adjustment, repair or replacement of functional components
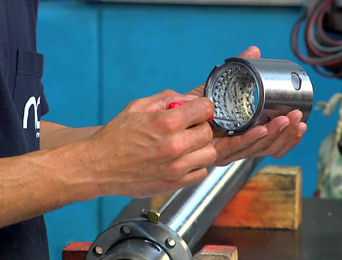
At NC SERVICE we inspect all the milling machine mechanical and electrical functional components, determining, in each specific case, the need to adjust, repair or replace each of these components.
Our highly-skilled engineers from the Engineering Department inspect, adjust, pre-stress and repair all the milling machine spindles (X,Y,Z), normally replacing all the bearings on each axis. All the screw drive belts and also the spacers, are also inspected to decide whether to repair or replace them.
With regard to the electric motors, these are studied on a case by case basis, to decide whether or not to repair the motor in question or replace it with a new one.
All the manual or automatic heads are inspected and repaired, looking at all the bearings, o-rings, electro-spindles, rods and sensors, and determining the need to either adjust or replace each one.
At NC SERVICE we also check and repair components such as seals, gears, bearings, hydraulic pump and unit, gear boxes, accumulators, torque transmission systems, etc. and, in general, any functional component of the milling machine required to guarantee the reliability and functionality of the milling machine.
4 Machining and grinding of components

At NC SERVICE we locate all the milling machine mechanical parts subject to wear during its life cycle, to subsequently analyse and determine the requirements with regard to the adjustment, repair or replacement of each mechanical part. Therefore, this basically involves the inspection and grinding of the tables and rams and, in general, those mechanical parts involving friction, in order to restore them to optimal condition.
At NC SERVICE we inspect all the guideways, checking their tolerance, repairing or replacing all the turcites which come in contact with these guideways at the metal joints. With regard to friction milling machines, in which the guide tolerance needs to be corrected, this is performed manually by hand scraping the guideways until the necessary tolerance is achieved in each case.
In this way, it is possible to return components to their initial operating condition, re-establishing the original productivity of the milling machine.
5 Cleaning and painting

After disassembling all the milling machine parts on its X, Y, Z axes, at NC SERVICE we then check all components, established the action to be taken for each specific part, with regard to cleaning, repair and painting.
The first step is to clean all the parts with pressurised water to that a meticulous inspection can then be made. Any dented or broken parts are either repaired or replaced, depending on the extent of the damage.
Once the parts have been inspected or repaired, they are then cleaned with a degreaser and re-inspected. Any slight dents found are repaired by applying a body filler. The parts are then sanded and a primer undercoat is applied, thereby ensuring that the top coat of paint will have a perfect finish, without it cracking or flaking off over time.
We finally apply the appropriate colour of paint to each part so that, once assembled, the milling machine looks just like new.
6 Replacing and upgrading the electrics / electronics
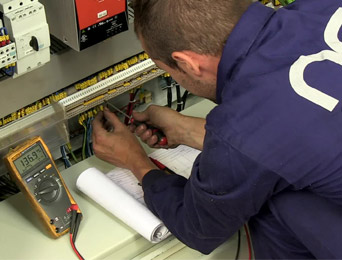
At NC SERVICE our retrofitting process goes beyond the mere mechanical restoration of our customers' milling machines, to include either the retrofitting or upgrading of the machine's electrics, electronics or numerical control. This part of the milling machine is generally the first to become obsolete. As a result, on occasions, the retrofitting solely involves these parts, with no mechanical refurbishment.
We either upgrade or replace all the milling machine electric or electronic components (such as transformers, drivers, power supplies, contactors, relays, variable speed drives, software, motors, electric system, etc.), the numerical control which is normally replaced by a latest generation model, and the sensor and measurement systems (rulers, encoders, temperature probes, limit switches, etc.). Normally, our team of highly experienced engineers completely replaces the obsolete electric cabinet on the milling machine, by making a new, up-to-date one in which new components are installed.
Furthermore, during the retrofitting process, NC SERVICE also offers our customers the possibility of upgrading their milling machine by incorporating new features that were not available when the machine was originally designed, so as to achieve improved performance and increased functionality, in order to become even more competitive on the market. Some of the upgrading tasks most frequently demanded by our customers are listed below:
- Replacement of the numerical control with a latest generation model
- Installation and commissioning of additional axes and divider plates
- Installation and commissioning of tool magazines and automatic changers
- Increased operating capacity (length and speed of travel, etc.)
- Installation of tool and workpiece measuring probes
- Installation of CNC-PC communication systems
- Installation of chip extractors
- Installation of tool cooling systems
- Installation of motor spindles
- Manufacture and installation of guards and safety devices
- Improved performance through the installation of new components
- Improvement in the PLC program
It should be emphasised that NC SERVICE always obtains the customer's agreement beforehand with regard to all the operations and parts to be either repaired or replaced during the retrofitting and upgrading work, based on the customer's needs and requirements.
7 Assembly and adjustment of the structural components

Once all the functional parts of your milling machine have been inspected and either repaired or replaced, and all parts have been repaired and painted, the next step in the procedure in place at NC SERVICE is to assemble all these components.
This enables us to make a final adjustment of all the milling machine's structural components in their final position and location, checking for the optimal functionality of each repaired, replaced or inspected part.
We assemble, check and adjust not only the mechanical components, but also all the electrics, electronics and control parts, resulting in a completely retrofitted milling machine, that has been thoroughly checked and offers our customers every guarantee of productivity and reliability.
8 Compliance with standards and regulations

The milling machine retrofitting process at NC SERVICE also involves any necessary upgrading to ensure that each machine complies with the standards and regulations in force. Therefore when, due to its age, the milling machine to be retrofitted is not fitted with the guards, raceways and other safety devices required in the CE regulations in force, then our Engineering Department will include all these safety requirements in the milling machine retrofitting process. This ensures that workers are always guaranteed adequate protection when operating these machines, thereby reducing the risk to these machine operators and to other workers as well.
We can also repair these parts on more recent milling machines should they be worn or damaged. Our customers can also request this machine upgrade to comply with the regulations in force, with no need to completely retrofit their milling machines.
9 Installation and commissioning

Once the retrofitted milling machine has finally been returned to optimal conditions, NC SERVICE then carries out the installation and commissioning work on-site at its customer's facilities.
This work is extremely important for optimising the future performance and output of the milling machine, primarily with regard to accuracy. For this reason, this work is performed with the utmost reliability and guarantee, making our extensive know-how, substantial experience and all our technical and human resources available to customers, given the great complexity of these machines.
10 Calibration, testing and acceptance by the customer

The final stage in the milling machine retrofitting process performed by NC SERVICE comprises tests to ensure that it is operating correctly, to the complete satisfaction of our customers.
Our skilled engineers check the geometry and levelling of the milling machine at the customer's plant and also calibrate its linear movements using a laser interferometer. Therefore, together with our customers, we always check that the machine is operating perfectly. Our work is only considered to be completed once we have guaranteed full customer satisfaction and the perfect performance of the machine, based on the accuracy required for the work to be performed.
Then, once the milling machine retrofitting process is considered to have been successfully concluded, this marks the start of the work included in our Preventive Maintenance contracts or our Technical Support.
Do you need to retrofit your milling machine?
Please complete this form and we'll contact you as soon as possible.